MATERIALES Y PROCESOS
TAXONOMÍA
Familia que reúne los procesos de moldeo, deformación y remoción de material.
FAMILIA FORMADO
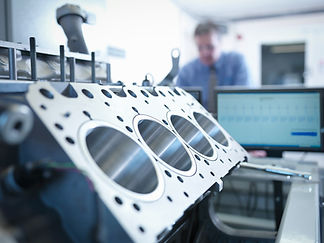
CLASE:
MOLDEO
Realización de una figura mediante un molde.
CONTACTO
Los procesos de fabricación de moldes abiertos o de moldeo por contacto permiten construir moldes en capas sucesivas. En el proceso de moldeo por contacto se superponen láminas de plástico o fibra de vidrio impregnadas en resina sobre la forma de un molde hasta que se consigue el grosor deseado. El moldeo por rociado es el proceso de polarización de plástico fundido sobre una forma o de polarización de resina sobre fibra de vidrio adaptada a una forma o un molde.
Materiales: Resinas. fieltro de bajo gramaje y fibra de vidrio
EMPAREDADO
Las características que definen a un molde sándwich, son las dos superficies de separación. Un molde sándwich, no requiere mucha más presión de cierre de la máquina que un molde sencillo de una sola línea de partición, ya que la superficie proyectada de las cavidades, en ambas caras de la placa, cancelan sus fuerzas. Como regla empírica, si tomamos el área de la superficie proyectada y la multiplicamos por la presión de la masa y el resultado a su vez lo multiplicamos por un factor de 1.1, determinaremos la presión de cierre necesaria para un molde sándwich.
Materiales: Polímeros termoplásticos, polietileno,polipropileno, PVC, cerámicos.
TRANSFERENCIA
Es un proceso de moldeo de piezas de material compuesto (fibra con resina), desarrollado a partir del moldeo por inyección de resina en un molde cerrado que contiene la pre-forma de la fibra.
Permite conseguir unas piezas finales con muy buenas propiedades estructurales debido a que es capaz de obtener, si se realiza correctamente el proceso, unos volúmenes de fibra muy elevados (mayores del 70%) con un volumen de poros (posibles orígenes de grietas y pérdidas de propiedades) muy pequeño (menor al 1%)
Las principales ventajas son:
-
Se pueden moldear piezas muy complejas con inserciones largas y complicadas.
-
Se pueden moldear piezas que tienen secciones gruesas y delgadas al mismo tiempo.
Las desventajas de este método son:
-
Los moldes son más caros que para el moldeo por compresión.
-
Hay mayor desperdicio del material, ya que los sobrantes no se pueden procesar.
Materiales: polímeros, termo endurecidos
COMPRESIÓN
Es un proceso empleado con los plásticos termofijos, ya que existen procesos más rápidos para los termoplásticos: Consiste en depositar ciertas cantidades del material en estado granulado o bien preformado en tabletas en la cavidad inferior del molde metálico; es continuamente calentada mediante vapor o electricidad.
El molde inferior se eleva y se pone en contacto con la mitad superior que también se calienta, se aplica presión mediante un cilindro hidráulico, lo que causa que el plástico fluya en la cavidad del molde y se conforme la pieza. Después de la compresión, la pieza se solidifica, se saca de la matriz. Las presiones de compresión pueden variar entre 140 a 700 Kg/cm., según el tamaño y la configuración de la pieza. Las temperaturas del molde varían de 60 a 120° C., dependiendo también del material de relleno.
Algunos materiales termoplásticos se procesan por compresión, para el ciclo de calentamiento y enfriamiento rápido del molde aumenta la dificultad en el uso de tales materiales, a menos que el molde se enfrié suficientemente antes de la expulsión, hay peligro de torcedura de la pieza.
Las ventajas del proceso son:
-
Poco desperdicio del material.
-
Bajo costo de acabado y obtención de piezas grandes.
-
Las desventajas del proceso son:
-
La dificultad de obtener formas intrincadas (bordes, agujeros pequeños).
-
La dificultad de obtener tolerancias más cerradas de +0.13 mm. y -0.13 mm.
Materiales: Polímeros, plásticos, reforzados en fibra de vidrio, plásticos termo rígido.
INYECCIÓN
El moldeo por inyección es el proceso más usado para la manufactura de componentes termoplásticos. En este proceso, el plástico fundido se fuerza hacia la cavidad de la matriz metálica que se ha maquinado a la forma del producto deseado.
Cuando el plástico ha solidificado lo suficiente, se abre la matriz y se extrae la pieza. El material plástico crudo se coloca en forma de bolitas en la tolva de la máquina. Luego entra al calentador en donde se funde. El plástico fundido se empuja entonces hacia la cavidad del dado mediante aplicación directa de presión hidráulica o mecánica.
Las ventajas de este proceso son:
-
Ahorro del material, espacio de fabricación y tiempo de producción.
-
Exactitud de forma y dimensiones de las piezas inyectadas.
-
Posibilidad de formación de orificios e inserción de elementos de otros materiales con los que la producción se hace completa.
-
Superficie lisa y limpia de las piezas inyectadas.
-
Buenas propiedades de resistencia.
-
Rápida producción de gran cantidad de piezas.
Las desventajas del proceso son:
-
No recomendable para baja producción a causa del alto costo herramental.
-
Las resinas pueden solidificarse antes de llenar el molde cuando se trata de secciones muy delgadas.
-
Piezas complicadas aumentan el costo herramental.
Materiales: Metales, cerámicos y polímero
SOPLADO
Moldeo por soplado de extrusión continua:
En el proceso continuo, un extrusor estático plastifica y empuja el polímero fundido a través del cabezal para formar un parison continuo. Para moldeo por soplado de partes de gran tamaño, se utilizan acumuladores para evitar el pandeo del parison.
-
Moldeo por soplado intermitente:
En el proceso intermitente, el fundido se acumula en el barril y se impulsa hacia fuera en un solo disparo. El moldeo por soplado intermitente se utiliza, entre otras aplicaciones, en la fabricación de botellas para lácteos, debido a su alta velocidad de producción.
-
Moldeo por soplado de coextrusión:
El moldeo por soplado de coextrusión posibilita la combinación de materiales con diferentes propiedades para crear un producto final más adecuado para una aplicación específica. Este proceso puede utilizarse para fabricar productos que contienen varias capas. Las diversas partes de la estructura pueden optimizarse para el mejor equilibrio entre propiedades y costo.
-
Moldeo por soplado por inyección:
El moldeo por soplado por inyección comienza con un preformado moldeado por inyección que luego se recalienta y se utiliza para darle su forma final en un molde.
-
Moldeo por soplado por inyección y estiramiento:
El moldeo por soplado por inyección y estiramiento comienza con un preformado moldeado por inyección que se recalienta y se estira con un cilindro mientras simultáneamente se sopla en un molde. Este proceso de conversión generalmente se utiliza para producir botellas PET.
-
Moldeo por soplado en 3-D:
El moldeo por soplado en 3-D es un desarrollo reciente en el que un brazo robótico se utiliza para posicionar el parison en un molde tridimensional antes de ser soplado. Las ventajas son poca cantidad de recortes y la posibilidad de producir formas complejas. En general, se utiliza para producir auto partes.
PLUVIMETALURGIA
La pulvimetalurgia o metalurgia de polvos es un proceso de fabricación que, partiendo de polvos finos y tras su compactación para darles una forma determinado, se calientan en atmósfera controlada para la obtención de la pieza.
Materiales: etalespuros, hierro, cobre, estaño, aluminio, níquel, titanio, aleaciones como latones, bronces, acero y aceros inoxidable o polvos
VACIADO
El vaciado es un procedimiento en varios pasos para la fabricación de esculturas, piezas completas o partes, relieves, etc. de metal, plástico, yeso, barro, cerámica, etc. Se consigue vertiendo (vaciando) una colada, en el interior de un molde, de algún plástico líquido solidificante, de yeso o metal fundido. Se diferencia del proceso de inyección, que también usa moldes, en que el molde se llena por el peso del material de relleno, usándose a veces la fuerza centrífuga para ayudar a llenar el molde. En contraposición, en el proceso de inyección, se usa un elemento mecánico para aumentar la presión del material de relleno del molde (pistón, tornillo sin fin, bombeo, etc.). En muchos de los métodos de vaciado no se destruye el molde o el modelo, pero en otros sí, por ejemplo, vaciado a la cera perdida donde se destruye el modelo y vaciado en arena, donde se destruye el molde cada vez.
Materiales: Polímeros.
Cables, Bobinados, Filamentos
Cables, microcomponentes de alta calidad
Cables
Cables , microcomponentes
Cables, laminas conductoras
Recubrimiento de cables
Recubrimiento de cables, protoboards
Recubrimiento de cables y circuitos electronicos
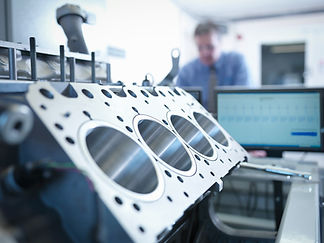
CLASE:
DEFORMACIÓN
Es el cambio en el tamaño o forma de un cuerpo debido a esfuerzos internos producidos por una o más fuerzas aplicadas sobre el mismo o la ocurrencia de dilatación térmica. Hay que destacar que es un proceso de conformado de metales en el que no se produce arranque de viruta, con lo que se produce un importante ahorro de material respecto a otros procesos, como por ejemplo el mecanizado.
FORJADO
La forja es un procedimiento de conformación por deformación que se realiza sometiendo al metal a esfuerzos violentos de compresión repetidos, una vez calentado a temperaturas superiores a la de recristalización, pero inferiores a las de fusión.
A estas temperaturas no sólo puede darse a los metales grandes deformaciones con pequeños esfuerzos; sino que la magnitud de la deformación es prácticamente ilimitada, sin que se produzca nunca acritud.
También se puede realizar un forjado en frío cuando se producen pequeñas piezas por martilleo (tornillos, varillas, arandelas, etc.) o cuando se quieren mejorar las propiedades mecánicas de los metales. En el forjado en frío las máquinas empleadas son prensas de mayor potencia que las empleadas en el forjado en caliente
La forja puede ser:
-
Forja libre esta no impone ninguna forma específica a la herramienta.
-
Forja con estampa (estampación) esta requiere la construcción de una estampa que reproduce la forma y dimensiones de la pieza a forja. Estampado (sujetado) con forja y forjado radial Son procesos de forjado que se usan para reducir el diámetro de un tubo o barra sólida. El estampado se ejecuta frecuentemente sobre el extremo de una pieza de trabajo para crear una sección abusada.
Materiales: Metales puros, aluminio, cobre, titanio, zinc y aleaciones en acero, aluminio cobre, magnesio y bronces
LAMINACIÓN
Es un procedimiento que consiste en modificar una masa metálica haciéndola pasar entre rodillos superpuestos, que giran en sentido opuesto. Se efectúa normalmente en caliente; sin embargo, existe la laminación en frío. En la laminación en frío los metales adquieren acritud al deformarse, por lo que se someten a un tratamiento de recocido al final de la operación, e incluso en una etapa intermedia.
Tren de laminación: es una agrupación de varios laminadores o cajas relacionadas entre sí, de modo que el material a laminar pasa sucesivamente por cada una, hasta completar el ciclo de elaboración.
Un laminador elemental estaría constituido por las siguientes partes: dos o más cilindros, normalmente horizontales; un bastidor que soporta los asientos de los cilindros; y un sistema de ajuste de los cilindros formado por espárragos roscados, llamados tornillos de presión. Todo el conjunto recibe el nombre de caja de laminación.
Materiales: Laminación de aceros, anillos, cuerdas, engranajes, polvos, roscas y perfiles.
COLADA CONTINUA
Consiste en llenar un recipiente (cuba) con metal fundido procedente de un horno emplea do para obtener acero. El metal cae de la cuba y se introduce en un molde refrigerado sin fondo donde se solidifica y se obtiene así una tira continua de sección semejante a la del molde Esta tira cae en vertical y al apoyarse sobre unos cilindros, a medida que avanza, se va colocando horizontal hasta ser cortada mediante sopletes, que se mueven a la misma velocidad que la plancha.
EXTRUCCIÓN
Es la operación en la cual una masa de material dúctil fluye a través de un orificio por medio de un impacto o una fuerte compresión, ocasionada por un émbolo o punzón, para formar una pieza de sección constante, hueca o no, y cuya longitud depende básicamente de la aportación de material efectuada.
-
EXTRUSIÓN DIRECTA
Un tocho de metal se carga a un recipiente y un pisón lo comprime forzándolo a fluir a través de una o más aberturas que hay en un dado situado al extremo opuesto del recipiente. Un problema es la gran fricción que existe entre el tocho y la pared interna del recipiente. Esta ocasiona un incremento sustancial de la fuerza requerida en el pisón.
-
EXTRUSIÓN INDIRECTA
Es un procedimiento que consiste en modificar una masa metálica haciéndola pasar entre rodillos superpuestos, que giran en sentido opuesto. Se efectúa normalmente en caliente; sin embargo, existe la laminación en frío. En la laminación en frío los metales adquieren acritud al deformarse, por lo que se someten a un tratamiento de recocido al final de la operación, e incluso en una etapa intermedia.
Materiales: Metales: aluminio, cobre, plomo estaño, magnesio, zinc, acero, titanio. plomeros y cerámicos
TROQUELADO
CORTE O PUNZONADO:
El punzonado es la operación de troquelado en la cual con herramientas aptas para el corte se separa una parte metálica de otra. La lámina, para que pueda ser cortada con punzón de acero templado, debe tener un espesor menor o igual al diámetro del punzón.
EMBUTIDO:
Consiste en transformar una lámina de metal en un cuerpo hueco tridimensional en una o más pasadas. En la operación de embutir no se debe modificar el espesor de la lámina, aunque en la práctica esto no sea totalmente cierto. El troquel se debe lubricar para dar mayor fluidez al material y proteger las partes contra el rozamiento.
Materiales: Papeles de fibras, telas, cerámica, plásticos, caucho producto en madera y Metales, cuero, porcelanas.
ESTIRADO Y TREFILADO
Son dos procedimientos de conformación por deformación plástica casi idénticos que consisten en hacer pasar el material de aportación por una matriz o hilera de forma determinada. Es procedimiento se realiza en ambos casos en frío.
La diferencia entre ambos procedimientos consiste en el objetivo que se persigue
En el estirado se efectúa la reducción de la sección para obtener formas y dimensiones determinadas.
En el trefilado se desea reducir la sección (normalmente circular) al máximo.
Materiales. Vidrios, metales y polímeros.
TERMOFORMADO
El termoconformado o termoformado es un proceso consistente en calentar una plancha o lámina de semielaborado termoplástico, de forma que al reblandecerse puede adaptarse a la forma de un molde por acción de presión vacío o mediante un contramolde.
Materiales: Termoplásticos
DOBLADO
El doblado de metales es la deformación de láminas alrededor de un determinado ángulo. Los ángulos pueden ser clasificados como abiertos (si son mayores a 90 grados), cerrados (menores a 90°) o rectos. Durante la operación, las fibras externas del material están en tensión, mientras que las interiores están en compresión. El doblado no produce cambios significativos en el espesor de la lámina metálica.
Materiales: Metales ferrosos o termoplásticos
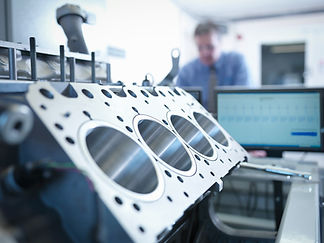
CLASE:
REMOCIÓN DE MATERIAL
Realización de una figura mediante un molde.
LIMAS
-
Limas para metal: éstas son de muy diversas formas y granulado. Si se hace una división según su sección existen:
-
Limas planas: con igual anchura en toda su longitud o con la punta ligeramente convergente: las superficies de corte pueden ser las dos caras y los cantos, pero también las hay sin corte en los cantos, es decir lisos, y que permiten trabajar en rincones en los que interesa actuar tan sólo sobre un lado y respetar el otro.
-
Limas de media caña: Tienen una cara plana y otra redondeada, con una menor anchura en la parte de la punta. Son las más utilizadas, ya que se pueden utilizar tanto para superficies planas como para rebajar asperezas y resaltes importantes o para trabajar en el interior de agujeros de radio relativamente grande.
-
Limas redondas: son las que se usan si se trata de pulir o ajustar agujeros redondos o espacios circulares.
-
Limas triangulares: sirven para ajustar ángulos entrantes e inferiores a 90º. Pueden sustituir a las limas planas.
-
Limas cuadradas Se utilizan para mecanizar chaveteros, o agujeros cuadrados.
MECANIZADO
Un proceso de mecanizado, se puede definir como un conjunto de operaciones necesarias para modificar las características de la materia prima. Estas características pueden ser de naturaleza muy variada tales como la forma, el tamaño o la estética.
Materiales: vidrios y piedras, acero, hierro, latón, bronce, cobre, aluminio. piedra, acrílicos, plásticos MDF, madera maciza. aglomerados, madera, polímeros metales ferrosos, no ferrosos y mármol.
TORNO
el torno es la máquina herramienta de mecanizado más difundida, estas son en la industria las de uso más general, la pieza se fija en el plato del torno, que realiza el movimiento de corte girando sobre su eje, la cuchilla realiza el movimiento de avance eliminando el material en los sitios precisos.
TALADRO
La pieza es fijada sobre la mesa del taladro, la herramienta, llamada broca, realiza el movimiento de corte giratorio y de avance lineal, realizando el mecanizado de un agujero o taladro teóricamente del mismo diámetro que la broca y de la profundidad deseada
FRESADORA
En la fresadora el movimiento de corte lo tiene la herramienta; que se denomina fresa, girando sobre su eje, el movimiento de avance lo tiene la pieza, fijada sobre la mesa de la fresadora que realiza este movimiento
MORTAJADORA
Máquina que arranca material linealmente del interior de un agujero. El movimiento de corte lo efectúa la herramienta y el de avance la mesa donde se monta la pieza a mecanizada.
BROCHADORA
Máquina en la que el movimiento de corte lo realiza una herramienta brocha de múltiples filos progresivos que van arrancando material de la pieza con un movimiento lineal. Esta máquina es muy utilizada para hacer chaveteros o cuñero.
ESMERILADO
El esmerilado consiste en la eliminación del material, mediante la utilización de partículas de abrasivos fijas, que extraen virutas del material de la muestra. El proceso de extracción de virutas con un grano de abrasivo de aristas vivas provoca el menor grado de deformación de la muestra, proporcionando simultáneamente la tasa más alta de eliminación de material.
PULIDO
El pulido, como proceso, se ha descrito ya anteriormente junto con el esmerilado. El pulido incluye los últimos pasos del proceso de preparación. Utilizando de forma sucesiva tamaños de grano cada vez más pequeños y paños cada vez más elásticos, el pulido permite eliminar todas las deformaciones y rayas provocadas por el esmerilado fino. El riesgo del pulido radica en la aparición de relieves y en el redondeo de los bordes, como consecuencia de la elasticidad de los paños. Dichos inconvenientes se reducen utilizando unos tiempos de pulido tan cortos como sea posible